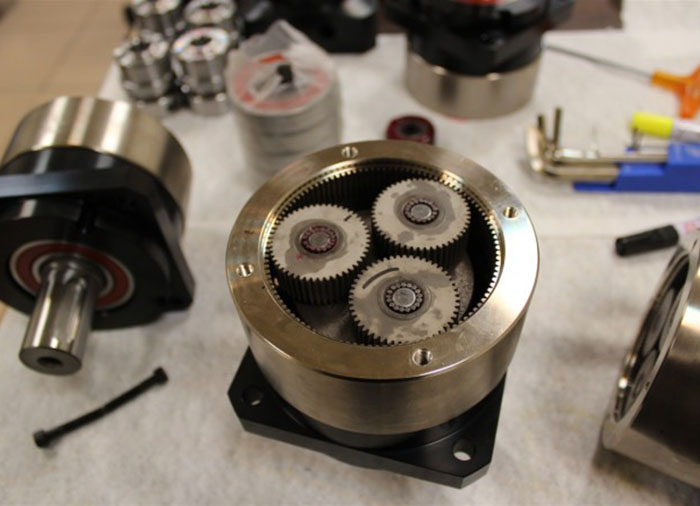
- 11月 1, 2020
- News
- 0 Comments
With the continuous development of the gearbox industry, more and more enterprises are using planetary gearbox, planetary gearbox is an industrial product, planetary gearbox is a communication mechanism, its structure is tightly integrated by an inner tooth ring on the tooth box housing, ring tooth center has a self-driven solar gear, between the two have a set of three gears and other components combined in the The planetary gear set on the tray, which relies on the force shaft, inner ring and solar tooth support to float during the period, when the force side power drives the solar teeth, can drive the planetary gear rotation, and follow the trajectory of the inner ring along the center of the public, the planetary rotation drives the output power linked to the outer force shaft of the tray.
Compared with other gearboxes, planetary gearboxes are characterized by high rigidity, high precision (up to 1 minute for a single stage), high transmission efficiency (97%-98% for a single stage), high torque/volume ratio, and lifetime maintenance-free. Most are mounted on stepper and servo motors to reduce speed, lift torque, and match inertia.
Today GearKo to tell you which factors will affect the precision planetary gearbox and some other transmission equipment transmission accuracy.
The main source of error for the transmission accuracy of the gearbox transmission chain
The transmission chain in general machinery and equipment is composed of gears and gears, gears and braces, worm wheels and worms, screws and nuts. Throughout the drive chain, the transmission error is transmitted from the power input link to the terminal acter and accumulated according to the drive ratio. The transmission accuracy of the transmission chain has obvious influence on the processing error of the drum processing thread and the rolling gear of the roller. The transmission accuracy of the walking gearbox refers to the degree to which the precision of each link affects the accuracy and uniformity of the movement of the terminal executor in the transmission chain. During equipment maintenance, the common sources of error for transmission accuracy are:
(1) The error of the transmission part has a major influence on the transmission accuracy of the equipment.
(2) The error of matching parts and their assembly quality have a significant effect on transmission accuracy.
(3) The transmission parts in the work, due to heat, force, inevitably to cause deformation, the transmission chain will also have a certain impact on the transmission accuracy.
2. The main error source of guide accuracy of the guide rail
The guidance accuracy of the guide rail refers to the accuracy of the motion trajectory when the moving parts of the mechanical equipment move along the guide track. In addition to the type, combination form and size of the selected guide in the design, the main factors commonly found in equipment maintenance are:
(1) affected by the appropriateity of the rail clearance.
(2) Affected by the stiffness of the rail itself.
(3) Affected by the geometric accuracy of the guide rail.
The adjustment of mechanical equipment such as planetary reducer is mainly to make the equipment have reasonable working precision and normal working function by selecting the appropriate fit relationship between the parts. Therefore, in general, the adjustment of machinery and equipment can not be carried out only after the assembly of components. This issue must be considered from the time the equipment fault is analyzed and the part in question is determined to be repaired.
3. The main error source of the spindle rotation accuracy of the reducer
Spindle swing accuracy refers to the radial round beat of the working parts at the front of the spindle, the size of the end face round beat and axial movement. The main error sources for spindle swing accuracy are as follows.
(1) The processing error of matching parts and the quality of their assembly
1) There is a parallelity error at both ends of the bearing bushing behemoth.
2) In the assembly, whether the bearing gap adjustment is suitable or not has a significant effect on the spindle swing accuracy.
3) The bearing hole on the gear deceleration chassis has a roundness error, the dimension error when matching with the bearing collar, and the verticality error between the axial positioning end face and the middle axis of the hole.
4) The nut that locks and adjusts the bearing gap on the main shaft of the walking reducer has the end plane degree error, the verticality error between the nut end face and the thread center axis, the connection error between the thread, etc.
(2) The processing error of the spindle
1) The shaft neck has a roundness error.
2) The axial positioning surface of the bearing has a vertical error with the spindle axis.
3) There is coaxial error between the two shaft necks on the spindle.
4) The spindle taper hole has coaxial error relative to the shaft neck.
(3) Bearing processing error
1) There are dimensional errors and roundness errors between the rolling bodies of rolling bearings, eccentricity of the inner round hole relative to the rollers, roundness errors between the inner round rollers, coaxial errors between the front and rear bearings, etc.
2) Sliding bearings have the roundness error and coaxiality error of the inner and outer circles, the coaxial error between the front and rear bearings, and the dimensional error between the bearing hole and the shaft neck.